Calculation software helps with life-time estimation according to Arrhenius
Assessment of the long-term behaviour of new sealing materials
When it comes to new requirements, for example for meeting the current “evaluation criteria for plastics and other organic materials in contact with drinking water” [1] – abbreviated to “KTW-BWGL” – (previous designation “Elastomer Guideline” [2]), then it always also involves new or modified materials. However, the focus is not only on the new hygienic properties which have to be met but also, and quite naturally, on the maintenance of technical requirements. In the case of concealed gas and water pipes for domestic distribution systems or in the case of underground supply lines, the fact that the long-term properties of elastomer seals must not deteriorate makes things even more difficult. But how certain can one be that the new materials at least achieve the required life-time of the previous materials or, better still, exceed it? Before any changeover, therefore, the new materials should be compared with the old ones and evaluated on the basis of reliable testing.
State of the art
In a first approximation, the life-time of elastomer materials is estimated in accordance with the laws of Arrhenius. The state of the art is described in ISO 11346 [3].
A brief description of the method
A number of material samples are stored at three elevated temperatures at least and the times taken to reach the threshold value*) of a property relevant to function, e.g. compression set (CS), are measured and then subsequently represented in summary graph form (Fig. 1).
The time-temperature value pairs obtained in this way at the threshold value (in Fig. 1 this is the horizontal red line at 70 %) are represented linearly using the Arrhenius equation and then extrapolated to the application temperature (e.g. 25° C) (Fig. 2).
The result of the extrapolation up to the application temperature in this example: at a constant 25 °C the limit CS of 70 % is reached after 3,126,015 hours (= 358 years).
Comparability – the aim of a standard
In contrast to many other standards which are being used today in test laboratories and for which repeatability and comparability are of extreme importance, ISO 11346 [3] allows a surprisingly high degree of freedom. As a consequence, in many cases the calculation results are not comparable with each other.
The reason for this is explained in the following points:
It is actually also possible, in coordination with the client, to shorten the testing times in order to save time and costs. However, by so doing test results are obtained which have not been determined in line with standards and so cannot be used as a basis for a qualified estimation of life-time. So what is the value of a test result like this?
It is not surprising therefore that calculation results – depending on the test laboratory and the client’s specifications – on one and the same material can differ significantly from each other, even though tested in accordance with ISO 11346 [3]. It is expected of a standard here that all test parameters are described as precisely as possible so that everyone obtains comparable results.
Other standards relating to life-time estimation, improvement potential for practical application
Estimation of life-time, among other things, is also described in EN 549 [4]. It also refers to the principle according to ISO 11346, but it specifies a range of calculation parameters very much more precisely. However, for one thing this standard is specially designed for static sealing materials, therefore the focus lies on the compression set as the test parameter, and for another thing the explanation of the calculation method is not represented in a way which is more transparent. However: with very good expert knowledge and by spending a great deal of time, it is possible to conflate the calculation parameters described in EN 549 [4], such as the statistical tolerances for the measurement ranges and best-fit curves and the mathematical correlations for example, into a calculation programme and develop a piece of software.
Basically, the function threshold value and application temperature are product-specific parameters which, of course, each client determines individually – regardless of the specific conditions of application. It is not possible to regulate this by means of a standard. These specifications therefore have to remain variable. Comparability can nevertheless be established provided that the tests on the material to be compared are performed up to the same threshold value as the reference. Calculating the results at the application temperature is then merely a mathematical exercise.
A realistic life-time estimation is then achieved if, instead of assuming a constant temperature for the calculation, reference is made to a specific climate. After all, a constant temperature over the course of a year only exists in extremely special cases in practice. For example, the time-temperature collective for a gas pipeline in the open and exposed to direct sunlight, such as in Seville, differs considerably from a drinking water pipeline laid 1.20 m below ground. Depending on the application, therefore, the time-temperature collectives can turn out to be extremely diverse. Therefore calculations should be based on climate profiles which are acquired on the basis of sound practical measurements taken over the course of a year. They should be as close as possible to reality.
These days there is an increasing tendency to describe practical time-temperature collectives for the most widely varying application scenarios, such as for example
- for gas pipelines laid above ground in a hot climate: EN 549 [4] (Annex C, Table C.1)
- for pipelines laid underground: see [5]
- for hot water installations: ISO 10508 [6] (Table 1 Note a and Annex A)
Requirements concerning a user-friendly calculation programme
A calculation programme should offer the best possible convenience and reduce the risk of a defective calculation to a minimum. Even so, the user is still not spared the task of familiarising himself with the essential features and the requirements of ISO 11346 [3]. After all, the specifications must be thought about and taken into account before starting to carry out the tests. Because the first phase includes some very time-consuming tests, at the end of which no-one would like to find out that a further and even longer test cycle needs to be started.
The optimum programme helps the user from the outset, in other words during the current series of measurement results to be entered, in the following way:
Phase 1
a) Once the first 3 to 4 measurement points are present, it immediately allows a projection to be made on the test time to be expected so that, if necessary, corrective action can be taken at this early phase. This is of importance for the measurement series at the lowest test temperature.
b) It constantly checks the measurement results to be entered and indicates whether all test values are trustworthy with reference to the measurement ranges and so are usable.
c) Because of the error monitoring and the calculation parameters specified, the programme manages with only three test temperatures – an important cost consideration.
Phase 2 (Arrhenius calculation)
d) This allows an assessment of the trustworthiness and quality of the best-fit curve and it checks/verifies the applicability of the Arrhenius method.
Phase 3
e) After entering the time-temperature values for the application climate selected, or the application temperature, the programme calculates the life-time.
Long before the publication of the current version of EN 549 [4], Woco Pipe System Components (PSC) developed a calculation software programme based on the Arrhenius method and is offering this on a commercial basis. It has proved its worth many times over for the different materials and applications.
The software has been refined for years and is constantly adjusted to meet the current requirements of the relevant standards – such as ISO 11346 [3].
A practical example
The working stages described above can be illustrated as follows on the basis of a specific example with the aid of the Woco Pipe System Components (PSC) programme:
The assignment is estimating the life-time of a Tyton® sealing material for drinking water supply. The pipeline is buried at a depth of approx. 1.20 m. The sealing function is considered to be assured if, with a realistic time-temperature profile, the compression set (CS) is less than 55% after 150 years*).
The underlying time-temperature collective is to be determined with great care.
The application-specific time-temperature profile
The basis of the time-temperature profile specific to the application is the work of BÖHME & BÖTTCHER (2011) [7]. Figure 1 in this publication is represented here by Fig. 3.
The data from Figure 3 have been prepared for the temperature distribution at a soil depth of 1 m (see Table 1).
As the time-temperature collective for the assignment presented above, the temperature distribution over one year in Table 1 is to be used.
Preparation of the calculation concept
For the procedure for estimating life-time according to Arrhenius it is necessary first of all to clarify the most important boundary conditions, such as:
- The life-time to be expected: Determination of the test time until the threshold value is reached for the lowest test temperature. In our example: For an expected life-time of > 150 years the test time is at least 9 months.
- Selection of the function criterion: In the example, this is the compression set (CS). Note: According to [3], CS measurements should preferably be determined on the same test specimens. This results in a considerable reduction of testing effort and testing costs.
- The function threshold value as the pass-fail criterion for the maximum decrease of the functional characteristic. In the example, this is a CS value of maximum 55 %.
- The temperature load at which the life-time is to be calculated. In each case, a practical time-temperature profile is to be preferred over a constant temperature. In the example:
687 hours / 0°C
2672 hours / 5°C
1493 hours / 10°C
1669 hours / 15°C
2240 hours / 20°C (Table 1). - Note: The measurement programme is to be designed so that further application potential can be developed. This means not stopping the measurements as from a CS of > 55 %, as allowed by the specific application case, but at the earliest as from 70 %. Reason: For static seals, threshold value with a CS of < 70 % are permissible. The programme allows the life-time estimation with optional function threshold values, as long as one moves within the measurement value range with the three temperatures (interpolation). In the positive case, therefore, sealing systems with a permissible CS of up to max. 70 % could also be produced from the same material without further tests.
The first phase: The measurement programme
This consists of the CS measurements with a graphic representation of the value drop until the threshold value is reached at three different temperatures.
These temperatures should differ by approx. 20 °C in each case. Figure 4 shows the measurement sequence of T2 (80 °C) in our example.
Note: The test time at the lowest temperature is the time-determining factor (higher test temperatures result in shorter test times). Therefore it makes sense to start with this test. The programme extrapolates the time until the function threshold value is expected to be reached. After reaching the 4th measurement point it should be checked whether the threshold value – as specified (in our example > 9 months) – is exceeded within the permitted test time. If that is the case then testing is continued. However, if the test time is not reached, a new series of tests with adjusted temperature must be started.
Continual checking of the coefficient of determination shows up any possible measurement outliers. This enables the user to take corrective action even at a very early stage. Because it is only at the end of measurement (> 9 months) that it can be established whether reliable application according to the law of Arrhenius is possible. Hence, with this value monitoring, the quality and dependability of the measurement values are significantly raised and no nasty surprises are experienced after nine months.
The second phase: The Arrhenius calculation
Once the three measurement sequences are concluded, the programme independently calculates applicability according to the law of Arrhenius, once again by means of the coefficient of determination (R² > 0.98). Only if this condition is met can further computations be carried out reliably with the existing data material (Fig. 5).
The third phase: Estimation of life-time
There now follows the inputting of the time-temperature profile (Table 2) or the constant application temperature. In this way the programme calculates the life-time to be expected. The output takes place with a specification of the function threshold value and the time-temperature profile.
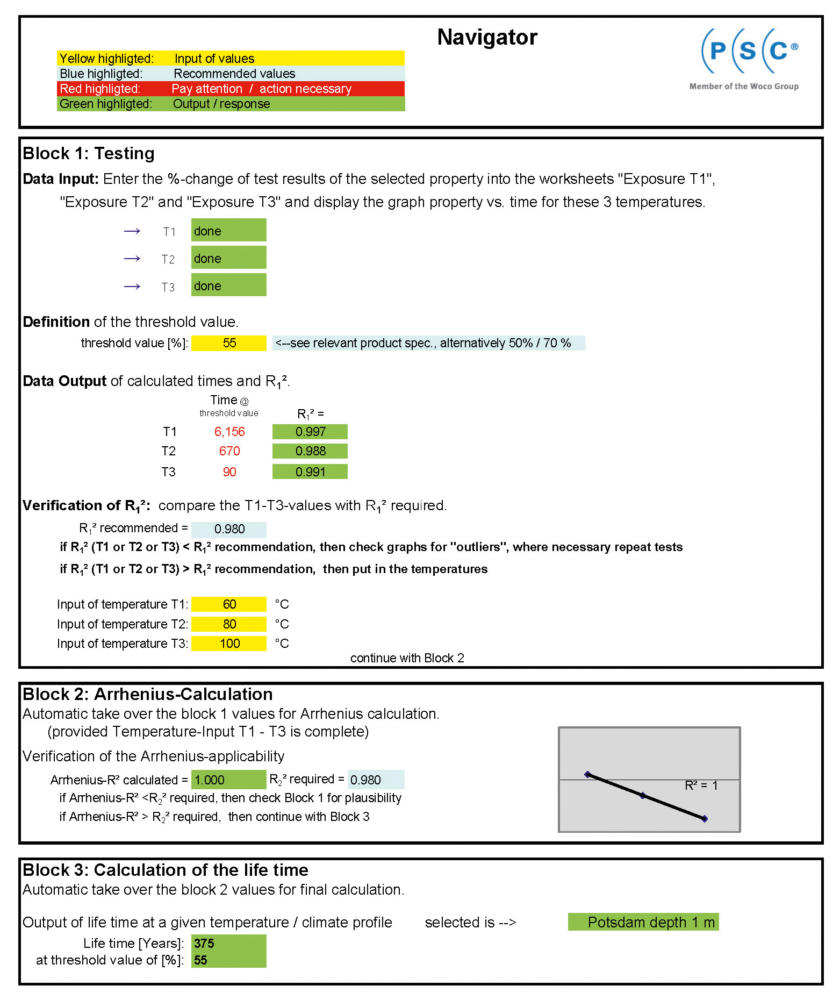
Fig. 6: Summary representation of all relevant data in the programme navigator.
The result of the estimation of life-time is presented in the programme navigator block 3 (Fig. 6).
The results output in block 3 means that, with the “Potsdam” time-temperature collective at 1 m depth for the sealing material, after approx. 375 years a CS value of 55 % will be reached.
Summary
With the Woco Pipe System Components (PSC) programme, the user has a tool available which enables him, for a fraction of the costs of a test laboratory, to perform a life-time estimation in accordance with [3](Arrhenius) independently and with simple means.
The costs of carrying out one’s own tests, using normal laboratory methods (e.g. CS) are manageable. Specimen calculation and references simplify the often so arduous path on the way to obtaining the results.
Should the end client require a test certificate from an accredited test laboratory, the user has significantly improved the prospects of a positive result. This is not merely a gain in terms of time, but it also represents a reduction in costs.
Bibliography
Authors:
Harald Hager, Woco IPS GmbH,
Joachim Albrecht, Woco GmbH & Co KG