Horizontal directional drilling
Single pipe pulling with ductile cast iron pipes
„The only constant is change, you just have to be able to react to it“. This quote from the Greek philosopher Heraclitus accompanied MIDEWA Wasserversorgungsgesellschaft in Mitteldeutschland mbH during the construction of a new DN 500 drinking water pipeline with ductile iron pipes between the eastern edge of the district town of Merseburg and the Werder waterworks. The damage caused by the Saale flood in 2013 made it necessary to replace the main supply pipeline for the town of Merseburg, its districts and the local industrial companies (e.g. Glaconchemie and APK AG).
The construction work was subsidised by the state of Saxony-Anhalt and the federal government as part of the „Flood 2013“ reconstruction aid.
Difficult framework conditions
The space available only allowed the damaged existing pipeline to be replaced along almost the same route, directly between the Werder waterworks and the feed-in point in the eastern part of the city. At the same time, however, this existing pipeline (DN 500 grey cast iron) had to remain in operation (approx. 500 m³ per hour) in order to ensure the supply of approx. 40,000 inhabitants. The fact that the work area to the east of the River Saale is located in the middle of a landscape conservation area and European bird sanctuary, which is also a designated flood area, also posed major challenges for all those involved in the project.
Modern technology, modern pipes
The old crossing of the Saale shipping channel was approved in 1961 (!) and then built using open construction methods with steel pipes in approximately 6 m deep water. Due to the current conditions (protected status of the construction site, proximity to the lock, operation of the existing pipeline, etc.), modern technology had to be chosen for the new drinking water pipeline. The innovative and environmentally friendly solution of a 750 metre long bore using controlled horizontal directional drilling (HDD) was quickly found. The HDD method was also the first choice in view of the difficult subsoil. The subsoil investigation revealed a layer of alluvial clay approximately 2 m thick in the floodplain area, followed by river gravel approximately 5 m thick, including tertiary clays/sands, and a further layer of claystone and sandstone several metres thick.
A borehole for professionals
The Halle branch of Umwelttechnik und Wasserbau GmbH won the tender in 2020 with the most cost-effective offer. Only a few companies in Germany have the drilling technology required for this project. Beermann Bohrtechnik GmbH, which specialises in horizontal directional drilling, was therefore chosen as a subcontractor. Their large HK 250 HT rig was used (Figs. 1 and 2).
Problems to be solved
The original plan was to drill two boreholes of approximately 750 metres each: the first for the backwash pipe, the second for the media pipe. The geology of the subsoil caused problems even during the pilot drilling, particularly with the backflow behaviour of the drilling fluid: Drill cuttings as well as dislodged gravel had to move with the suspension between the borehole wall and the drill pipe in the opposite direction to the drilling direction towards the starting pit. This ‘material transport’ is thought to have ‘blocked’ the gap in the area of the solid rock drilled through. The lack of return flow could therefore only be temporarily restored by various measures.
In the end, it was decided to replace the drill head at great expense, but this also proved to be impractical. Only with the help of a targeted relief borehole was it possible, after 680 metres of drilling, to reach the target pit directly in front of a school building. Thanks to the precise positioning of the drill head, the relief borehole was drilled with pinpoint accuracy. Continuing the drilling without reverse flow would have inevitably altered the soil structure around the drilling channel as a result of the drilling suspension introduced at high pressure, and would also have created stresses in the soil, thus endangering the important existing grey cast iron pipeline. Based on this experience, it was decided to use the borehole intended for the backwash line for the media line and to transport the suspension using suction trolleys. The “vacuum truck variant”, which had originally been rejected due to difficult access across a field, a construction project on the connecting road, close proximity to a school and limited space in the target pit, eliminated the need for an additional borehole and the associated loss of time.
The know-how
The pilot hole drill kit initially consisted of a 12” roller bit, jetting kit and steering tool, and the 6 5/8” drill string ( Figs. 3 and 4). The pilot hole was surveyed using a gyrocompass (Drillguide GST).
The 6 m deep Saale was crossed at a distance of 12m from the river bed. From the drilling site (85 m above sea level), the lowest point of the borehole (61.7 m above sea level) was well before the Saale, as the pipeline had to rise to 95 m below the river in a westerly direction, taking into account the spatial curve. In order to achieve this spatial curve, the entry and exit angles of the borehole were chosen to be relatively steep at approximately 15°.
After the pilot bore, the bore channel was widened to 970 mm in two passes and a cleaning run was carried out to reduce the risk of a lost borehole in these difficult ground conditions.
Parts of the drilling equipment.
(Source: vonRoll hydro (deutschland) gmbh & co kg, Wetzlar)
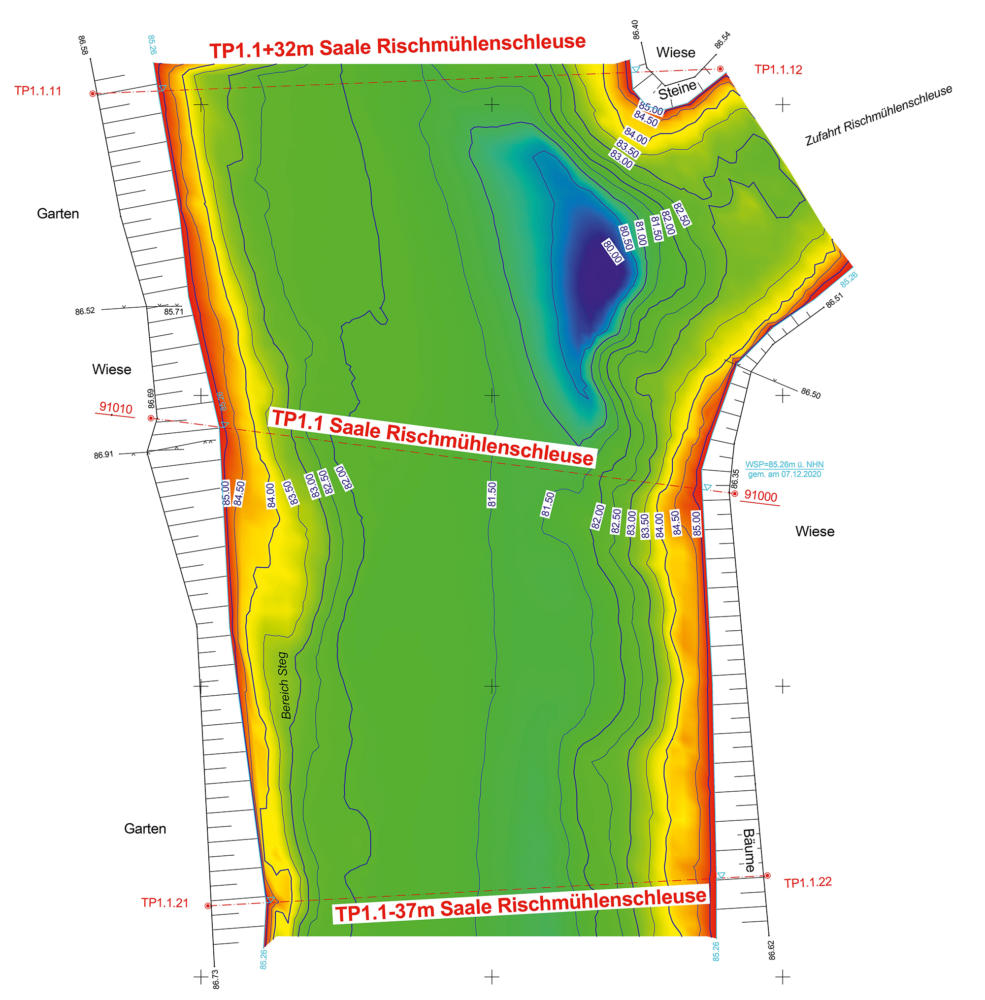
Plan of the depth contour of the river Saale in the crossing area before the start of construction.
(Source: MIDIC GmbH Mitteldeutsche Ingenieurconsult, Halle)
Pipe material from the professionals
The city of Merseburg had many years of good experience with the old existing grey cast iron pipeline. It was therefore an obvious choice to use cast iron for the new pipeline. Ductile cast iron pipes for drinking water supply in accordance with EN 545 [1] with a restrained BLS® socket joint and a cement mortar coating in accordance with EN 15542 [2] from von- Roll hydro (Germany) were the material of choice for the trenchless single pipe pulling method (Fig. 6). In the area of the pipe joint, the pipe joint protection is protected against mechanical damage by a push-over sheet steel cone (Fig. 7).
Last but not least, the high demands of the difficult ground conditions, the long pull-in length and, in particular, the installation conditions, even at low temperatures, as well as the expected long service life, were decisive for the use of ductile cast iron pipes.
The pipes were installed on an installation ramp during the tunnelling process (Fig. 8). The St Maximi city cemetery, which dates back to 1581 and is a listed historic monument, required this variant as it was located within the drilling axis on the opposite side of the road to the target pit.
The individual pipes in an HDD bore are connected to each other in a tension-locked manner – and there is no room for mistakes here, as there is no way of checking for leaks when laying individual pipes before pulling them in. A so-called barrel reamer (Fig. 9) was coupled to the drill string for the pull-in process and connected to the pulling head, which is connected to the pipe string, by means of a swivel joint.
A required pulling force of 380 kN, approximately 44% of the permissible tensile force of the pipe joint, was calculated in advance. In the end, almost twice as much pulling force was required, which was no problem for the BLS® DN 500 joint with a permissible tensile force of 860 kN.
The pipe was pulled in without interruption for almost 30 hours. Shift organisation with reserves, lighting at night, traffic safety, especially for pedestrians in the installation area, marking of the fixing points on the pipes and much more had to be taken into account in the preparations. This also included special pre-training of the fitters and continuous supervision of the pipe installation by the manufacturer (Figs. 10 and 11).
DN 500 ductile cast iron pipes with BLS® joint and cement mortar coating.
(Source: vonRoll hydro (deutschland) gmbh & co kg, Wetzlar)
Is running!
Following the pressure and hygiene tests (Fig. 12), the pipeline is now in operation. The work on the drinking water pipeline, which cost around € 3 million in total, has been completed. In addition to the main supply line, a pipe bridge (Fig. 13) with thermally insulated DN 400 ductile iron pipes (WKG) and over 1.1 km of smaller supply lines were built. The successful completion of the project was largely due to the constructive cooperation of all parties involved.
Authors:
Steffen Ertelt, vonRoll hydro (deutschland) gmbh & co kg
Thorsten Mahler, MIDEWA GmbH, Merseburg
Timo Mücke, Beermann Bohrtechnik GmbH, Hörstel
Jens Jünger, FICHTNER Water & Transportation GmbH, Leipzig